Problem Defined
Conveyor to Accommodate Irregularly Sized Parts Under Tight Time Constraints
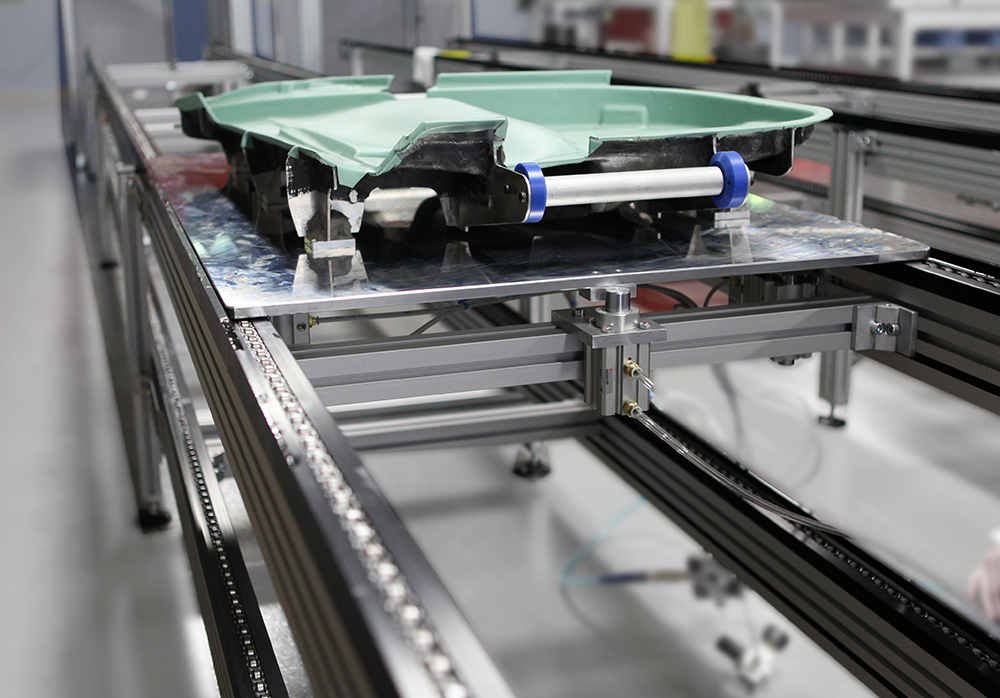
A leading automotive manufacturer came to mk North America for a solution to assemble front and rear car doors for a newly redesigned model. The doors were over-sized and had irregular conveying surfaces, and each door weighed up to 140 lbs. each. The customer also demanded a delivery time within 10 weeks.
mk North America's Custom Solution
Using Parallel Assembly Lines to Streamline the Assembly Process
The solution required a combination of mk’s GUF-P 2041 Flat-Belt Conveyors for the interior panel fabrication and mk’s VersaMove Plus Pallet Conveyor for the exterior door assembly.
Two parallel assembly lines were designed and built to process the left-side doors and right-side doors simultaneously with five Model GUF-P 2041 Flat-Belt Conveyors approximately 36” wide by 46” long to fabricate the interior panels. The interior panels are then delivered to two parallel mk VersaMove Plus SRF-P Over/Under Accumulating Roller Chain systems. Each VersaMove System is seventy feet long and includes seven work stations before the doors are removed for final assembly and the empty pallet enters the elevator to be lowered and returned for the next set of doors. Each system transports seven pallets, supplied by mk, and were each 30” wide by 47” long. Included in the system are precision stop & locate fixtures and lift & tilt features.
The entire system was designed, assembled, tested and shipped in 10 weeks ready for the customer to integrate their controls. mk North America delivered a combination of platforms from their standard designs with elements of the solution tailored to the customer’s unique requirements to meet their aggressive launch date.
Customer Benefits
- Two different types of conveyor systems delivered within 10-weeks
- Ability to convey a variety of different size parts on one system
- Compatibility between systems because both conveyors platforms came from the same supplier